|
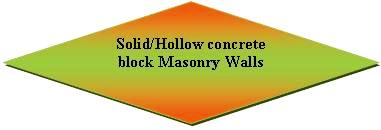
The concrete blocks in our country are in use for more than 30 years. Concrete offers flexibility in production which is not there in brick making. Also investment needed by way of land and capital is much less for the concrete block manufacture compared to the brick maker. Concrete blocks are produced in large variety of sizes either solid or hollow, dense or light weight, air cured or steam cured, load bearing or non load bearing can be produced manually or with the help of machines. Hollow blocks are defined as those blocks which have core wide area greater than 25% of gross area having one or more holes open at both sides.
|
The most commonly used concrete blocks have a nominal length of 40cm, height of 20cm and nominal width of 8,10,15 and 20cms. In addition a wide variety of non-modular blocks and special shapes are available in market for different purposes.
|
Materials for concrete blocks:
Cement : Ordinary Portland Cement, Rapid hardening Portland cement, PPC, can be used. The partial replacement of cement by a pozzolana i.e. rice husk ash, flyash etc is also permitted.
Aggregate : The maximum particle size of coarser aggregate is 13mm (10mm for hollow blocks). high proportion of fine aggregates are to be avoided as they increase the density.
|
Cement Aggregate ratio : The proportion of cement aggregate must be found be trails with different ratios such as 1:6, 1:8, 1:10 up to 1:16 by weight depending upon the application i.e load bearing or non load bearing.
|
Water cement ratio : Drinking water, should be used. As a simple test for cohesiveness, no excess water should be visible when a lump of concrete is squeezed in the hand, but if the sample is rubbed quickly on a smooth round metal bar or tube (2 to 4cm in dia), slight or film or paste should be brought to the surface.
|
Production:
Batching and mixing : Aggregates can be batched by volume or weight but by weight is more accurate. Cement should only be batched only by weight or using whole bags of 50 kgs. However, batching by volume using buckets etc is quite acceptable. The best Mixes are obtained with mechanically operated mixtures however; hand mixing if done should be on level smooth hard surface. Thorough mixing is essential to obtain cohesiveness. Since concrete begins to set within 30 to 60 minutes, only so much concrete must be prepared as can be used up before that happens.
Moulding : Concrete blocks can be moulded by several methods, ranging from manually tamping the concrete in wooden or steel mould boxes to large scale production with egg laying mobile machines and fully automatic stationery machines. The blocks are compacted by hydraulic or mechanical tamping machines and vibrated for few seconds with intervals with complete compactness. The quality of blocks generally increases with the degree of mechanization. The blocks are demoulded immediately after compaction.
|
Curing :
The blocks are left to set and harden for 24 hours and then stacked in layers. Curing is done for 21 days by water spray. Steam curing may be resorted for quicker strength development.
|
Solid and Hollow blocks possess several advantages such as economy, pleasing appearance, improve thermal comfort and reduced self weight.
|
The BIS prescribes a minimum strength of 20 kg/cm2 for concrete blocks.
|
|
|